Marshall Lee Forbes
- Born: 23 Sep 1828, East Hartford CT
- Marriage (1): Susan C. Hall in 1849
- Died: 24 Apr 1891, Meriden CT
General notes:
Silverplater
Events in his life were:
- He appeared on the census in 1850 in Wallingford CT. Listed as a silverplater.
- He worked before 1855 as a silverplater in Wallingford CT
- He worked circa 1855-1870 as a silverplater in Meriden CT as a principle of the MERIDEN BRITANNIA COMPANY. His invention of sectional plating was a major innovation in the production of quality plated flatware.
- He appeared on the census in 1860 in Meriden CT. Listed as a silverplater.
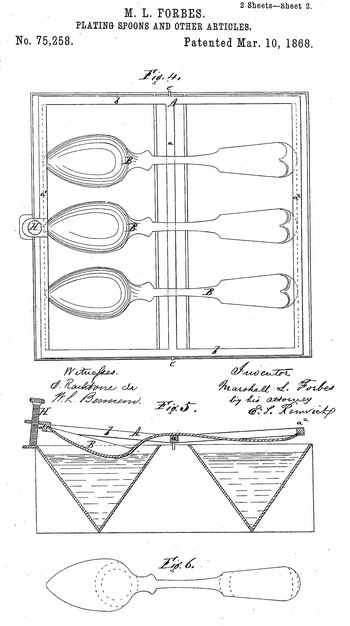
- Patent: 75,258, on 10 Mar 1868. MARSHALL L. FORBES, OF WEST MERIDEN, CONNECTICUT, ASSIGNOR TO THE MERIDEN BRITANNIA COMPANY OF SAME PLACE.
Letters Patent No. 75,258, dated March 10, 1868.
IMPROVEMENT IN PLATING SPOONS AND OTHER ARTICLES.
To All Whom It May Concern:
Be it known that I, MARSHALL L. FORBES, of West Meriden, in the county of New Haven, and State of Connecticut, have invented a new and useful Process and Means of Plating Spoons, Porks, and Similar Articles; and that the Following is a full, clear, and exact description and specification of the same.
The object of my invention is to coat spoons and similar articles with a plating or covering-metal in such manner that the thickness of the plating-metal shall vary at different parts of the articles, as desired, the thickness being greatest upon the parts most exposed to wear. To this end my invention consists of the method of coating the article unequally in the desired manner by immersing different portions of such article for different periods in the depositing-bath of an electro-plating apparatus with which said, article is connected, whereby the parts which are immersed for the longest period have the plating-metal deposited thickest upon them.
My invention consists, further, of the combination of a holder, adapted to confine the articles to be coated, with regulating mechanism by means of which the articles may be partially immersed to the required extent in the depositing-bath.
My invention consists, further, of the combination of said holder (adapted to confine the articles to be coated) with mechanism by means of which it may be tilted for the purpose of varying the extent to which the articles are partially immersed in the depositing bath.
My invention may be carried into effect in various ways, and the accompanying drawings represent two apparatuses adapted to the purpose—
Figures 1, 2, and 3 representing respectively a plan, side view, and transverse section of an apparatus of one form, and
Figures 4 and 5 representing a plan and transverse section of an apparatus of a different form.
The holder A in each of, said two apparatuses is adapted to the dimensions and form of the article, which in these examples is a teaspoon, B, and the holder consists of three bars, a a1 a2, connected by side-pieces bb. The two side-bars a1 a2 are formed with rebates to receive respectively the point of the bowl and the end of the handle of the spoon, and the central bar a is so placed relatively to the other two that the spoons are sprung over it when they are inserted in the holder. This holder is fitted at its ends with trunnions or pivots c c, on which it may be tipped, and the trunnions of the holder in figs. 1, 2, and 8, are supported upon adjustable bearings DD, which are connected with the ends of the depositing-bath or tank E by means of screws f, which pass through slots in the shanks of the bearings; hence, by raising or lowering these adjustable bearings the depth to which the articles (carried by the holder) may be dipped into the liquid in the tank, and held there, can be regulated as desired. The holder A is also fitted with an adjusting-screw, H, whose point bears upon the rim of the tank, so that by turning said screw the articles (carried by the. holder) may be tilted upon the trunnions cc, as axes, to vary the extent to which the said articles are dipped and held in the depositing-bath. In the form of apparatus represented in figs. 4 and 5, the regulation of the depth to which the articles to be coated are dipped, and at Which they are held in the bath, is determined by tilting them by means of the adjusting-screw; and this apparatus is adapted also to the progressive plating of the bowl and palm of the handle separately, the frame being tilted in one direction to plate the bowl and in the opposite direction to plate the palm. The form of apparatus represented in figs. 1, 2, and 3, is adapted to the progressive plating of both the bowl and palm of the handle, either simultaneously or separately, as found expedient. With either form of apparatus, the coating-metal may, if desired, be deposited upon a portion of the article in progressively diminishing or increasing areas, as indicated by the series of red lines upon the bowl of the spoon represented at fig. 6, or a patch of the coating-metal may be deposited of substantially uniform thickness. If the deposit is to be effected in progressively increasing areas, the distance to which the article is dipped is progressively increased during the operation of electro-plating, and vice versa if the deposit is to be effected in decreasing areas. When the articles have received the desired partial coating, they may be taken from the holder, and wholly immersed in the bath, and coated all over in the usual manner, or the articles may be first coated uniformly all over, and then have the thickness of coating increased at the desired parts by means of my invention.
Both apparatuses described afford an easy means of regulating the precise extent of the extra partial thickness of coating-metal, by regulating the depth of dip or partial immersion. Both also afford a ready means of conducting the galvanic current to the articles, as the holders are made of metal for that purpose so that the holder may be connected by means of a wire with one pole of the battery, while the plates of coating-metal immersed in the bath may be connected with the other pole of the battery in the usual manner. The holders represented are adapted to the confinement of spoons, and to holding three at a time, but they may be, varied in form to suit the articles to be held, and in extent to hold a greater or loss number of articles, as found expedient, it having been found expedient, when operating upon a large scale, to make the holder long enough to extend from one side to the other of the depositing-bath of the electro-plating-apparatus which may be constructed in the usual manner.
Having thus described the modes in which I have practised my invention, what I claim, and desire to secure by Letters Patent, is—
The mode, substantially as before set forth, of coating spoons and similar articles, with a regulated unequal thickness of the plating-metal by immersing different portions of the article for different periods in the bath of the electro-plating apparatus with which the article is connected.
Also, the combination of a holder, adapted to confine the article to be coated, with regulating-mechanism to hold the articles partially immersed to the required extent in the depositing-bath, substantially as before set forth.
Also, the combination of a holder, adapted to confine the articles, with mechanism for tilting the article, so as to vary the extent of immersion in the depositing-bath, substantially as before set forth.
In testimony whereof, I have hereunto set my hand, this eighteenth day of January, A. D. 1868.
Marshall L. Forbes
Witnesses:
James P. Platt
Orville H. Platt
- He appeared on the census in 1870 in Meriden CT. Listed as a silverplater.
Marshall married Susan C. Hall, daughter of Unknown and Unknown, in 1849. (Susan C. Hall was born on 18 Dec 1826 in Wallingford CT.)
|